WOOD WALL COMBO STATION
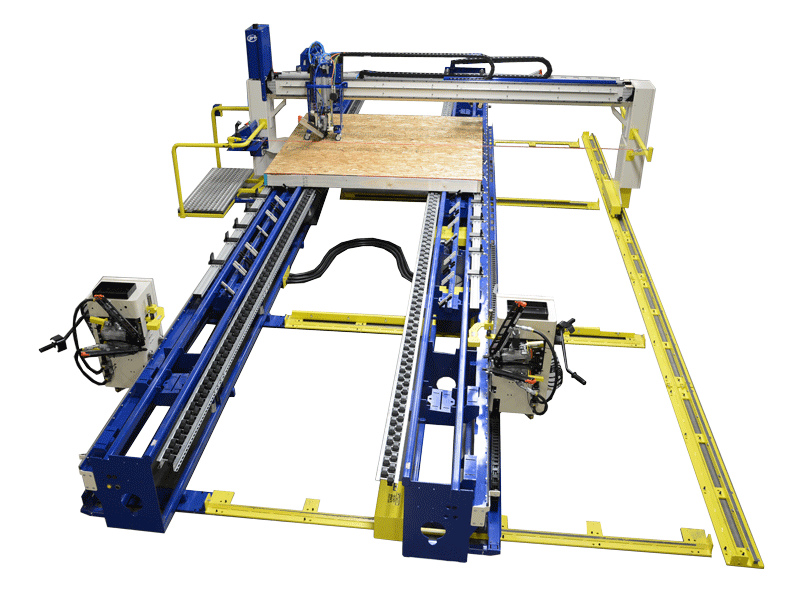
Quality Panels, Every Time
The Wood Wall Combo Station is an all-in-one system that frames, squares, and sheathes wall panels for quality panels every time. It is compatible with lumber from 2×3 through 2×10. Designed with the rigors of a panel shop in mind, our equipment is developed with longevity and quality. Many Panels Plus products built two decades ago are still in production today.
The Combo Station can be stand-alone or integrated into a full production line. Various sizes and configurations are available.
Benefits
- Ergonomic working height
- Improved squareness vs. traditional methods
- Superior wall panel consistency
- Flexibility with fastener spacing
- Fastens consistently and accurately
- Improved employee safety
Wood Wall Combo Station
The Combo Station is an all-in-one system that frames, squares, and sheathes wall panels. The Combo Station is designed for low-volume, entry-level operations and is ideal for companies that manufacture wood wall panels, such as off-site building manufacturers, manufactured home builders, and modular builders.
The Panels Plus wall panel systems are more ergonomic than traditional construction methods and are developed at an ergonomic working height. This eliminates the need to continually kneel or hunch over to build wall panels, improving employee health and safety.
How it Works
The Combo Station consists of a combo table, single tool sheathing bridge, and indexing tool carriages. The combo table is available with either stud locators or wide projection plates for stud placement. Stud locators offer quick and precise stud placement, while wide projection plates are designed for manufacturers equipped with a laser projection system, or for those using a plate-marking saw.
Once the studs are manually placed into the combo table, the wall panel is clamped against the squaring edge by stepping on the footswitch on the load end of the table or by push-button controls on the exit end of the combo table. This ensures the wood wall panel is square before fastening. The top and bottom plates are then fastened to the studs by using the indexing tool carriages.
Once the wall panel has been framed, the operator then uses the touchscreen on the sheathing bridge to preset fastener spacings. With the touchscreen, you can toggle between various presets and easily change the fastener spacing. The bridge is driven up and down the wall on a mounted v-track using the manual joystick. To assist in positioning the bridge at each stud, there is a laser pointer that projects a line on the plate where the fasteners are inserted.
When the wood wall panel is completed it is easily moved from the combo table using the pop-up conveyors that are operated using a second set of push-button controls. Power conveyors are an optional upgrade to move wall panels hands-free between workstations.
Make Hand Nailing A Process of the Past
The Combo Station comes equipped with indexing tool carriages and can also be purchased without. Indexing tool carriages eliminate the need to fasten wall panels by hand and allow operators to work at a safer ergonomic height.
When equipped, one tool carriage is attached to each side of the combo table on a rolling V-track. This semi-automated system fastens the top and bottom plates to the studs with the press of a single fire button located on the handlebar. The indexing tool carriages offer precise fastener placement taking the tools out of the operators’ hands – reducing safety issues.
When manufacturing wall panels by hand, fasteners can be spaced incorrectly or more fasteners can be used than what is required. With the Panels Plus indexing tool carriages, nail spacing is preprogrammed based on your company’s specifications – leading to exceptional panel consistency.
Wood Wall Combo Station Specs
Electrical | • 120Vac/60Hz/15amp |
Air | • 30 CFM @ 90-120psig |
Standard Machine Length and Width | • 33’ Long x 18’1” wide • Various sizes and configurations are available |
Wall Panel Size | • 4’6” to 12’4” H x up to 16’L • Various table sizes and configurations are available |
Compatible Materials | • Lumber from 2×3 to 2×10 |
Working Height | • 33’’ framing height |
Single Tool Sheathing Bridge | • Touchscreen • Joystick for bridge operation • Laser indicator for bridge alignment • Auto-return to the home position |
Sheathing Bridge Safety Features | • Emergency stop cables on each side of the bridge • Emergency stop button on the operator platform |
Indexing Tool Carriages (2) | • Semi-automated • Located on the stationary side & telescoping side of the table • Mounted on V-rail • Handlebars for easy operation • Fires nails into plates via the fire button on the handlebar • Offers precise fastener placement |
Table Features |
|
Telescoping Side | • Adjusted in and out to set panel height |
Stud Locators Option | • Located at 16’’ and 24’’ spacing • Color-coded for easy stud placement • Other spacings available • Ensures consistency with stud placement |
Projection Plates Option | • Provides a reference for laser projection • Offers a larger surface for stud and plate placement |
Squaring Edge | • Ensures squareness of wall panels |
Footswitch | • Located at the load end of the framing table • Clamps/unclamps the framing table |
Push-Button Controls (2 Sets) | • Located at the exit end and load end of the framing table • Set 1 – Clamps/Unclamps the framing table (on the exit end) • Set 2 – Pops up roller conveyors (on both ends of the table) |
Pop-Up Conveyors | • Extend the entire length of the table • Raised by push-button controls on either end of the table • Allows easy panel movement down the production line |